隨著科技的進步以及電子輔具技術的廣泛應用,為了樽節時間與金錢的成本支出,許多傳統的製造法則正迎來新的挑戰與嘗試,BMW Group Production(生產部門)近年便致力於 VR(虛擬實境) 與 AR(擴增實境)在造車上的應用性,他們計畫利用系統高度像真的特性在生產線上強化培訓、認證、流水線工作區規劃或者質量管理等各種用項目。
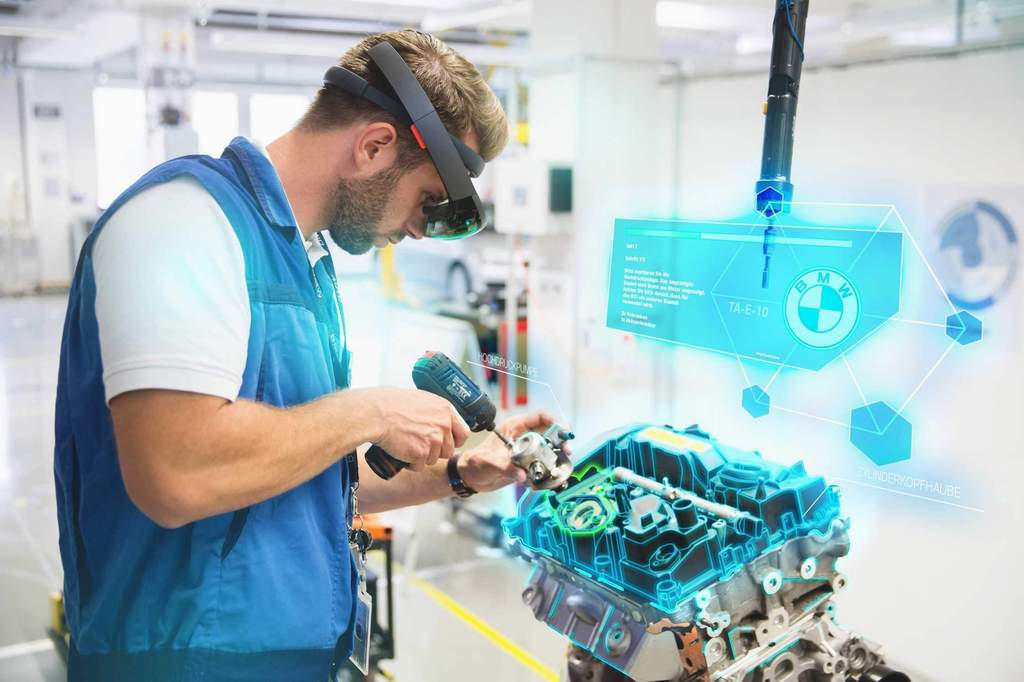
以工作區規劃來說,得益於VR技術,現在,建築、工廠工程、物流和裝配等領域的規劃人員可以與生產人員一起,完全虛擬地評估新生產區域,並在 3D 環境中測試新的生產流程,且可基於 3D 環境中的數位工廠數據進行規劃。
幾年來,BMW 集團一直在使用特殊的 3D 掃描儀和高識別度攝影鏡頭,以數位化方式捕捉工廠的結構,精確度達到毫米級,得到生產區域的三維圖像或散點圖,免去了複雜的數位重建工廠結構和現場手動記錄的需要。在規劃工作區或是整個裝配線上,BMW 集團業務部門亦將現有數據與虛擬庫相結合,該虛擬庫包括貨架、網箱、小型載重車以及其他 50 種常見運營資源等。
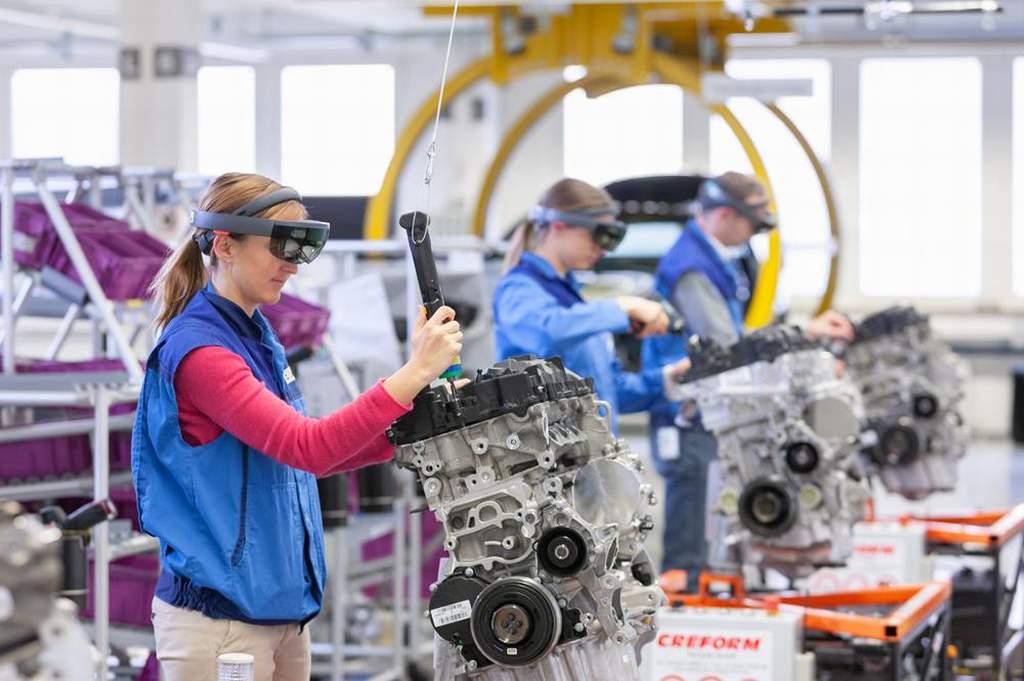
在人力的培訓和認證方面,BMW 在 Production Academy 可根據精益生產原則,對管理人員、生產規劃人員、生產流程負責人和質量專家進行培訓。然後,接受培訓的人員需要在產線傳授這些知識。現階段 AR 護目鏡已經在引擎裝配單元培訓課程中使用近 18 個月。
可視化的知識可指導參與者完成所有生產流程步驟並且提供具體信息,從而使參與者能按自己的進度工作,並通過語音控制確定培訓的速度。而且,在接受了監督進度的培訓師的快速指導後,可三人同時參加 AR 培訓。在此之前,一位培訓師只能一次培訓一人,現在利用新系統可同時培訓三人。而且,對參與培訓的人員的調查以及參與培訓人員的學習評估顯示,與進行傳統培訓課程相比,學習質量沒有差異。
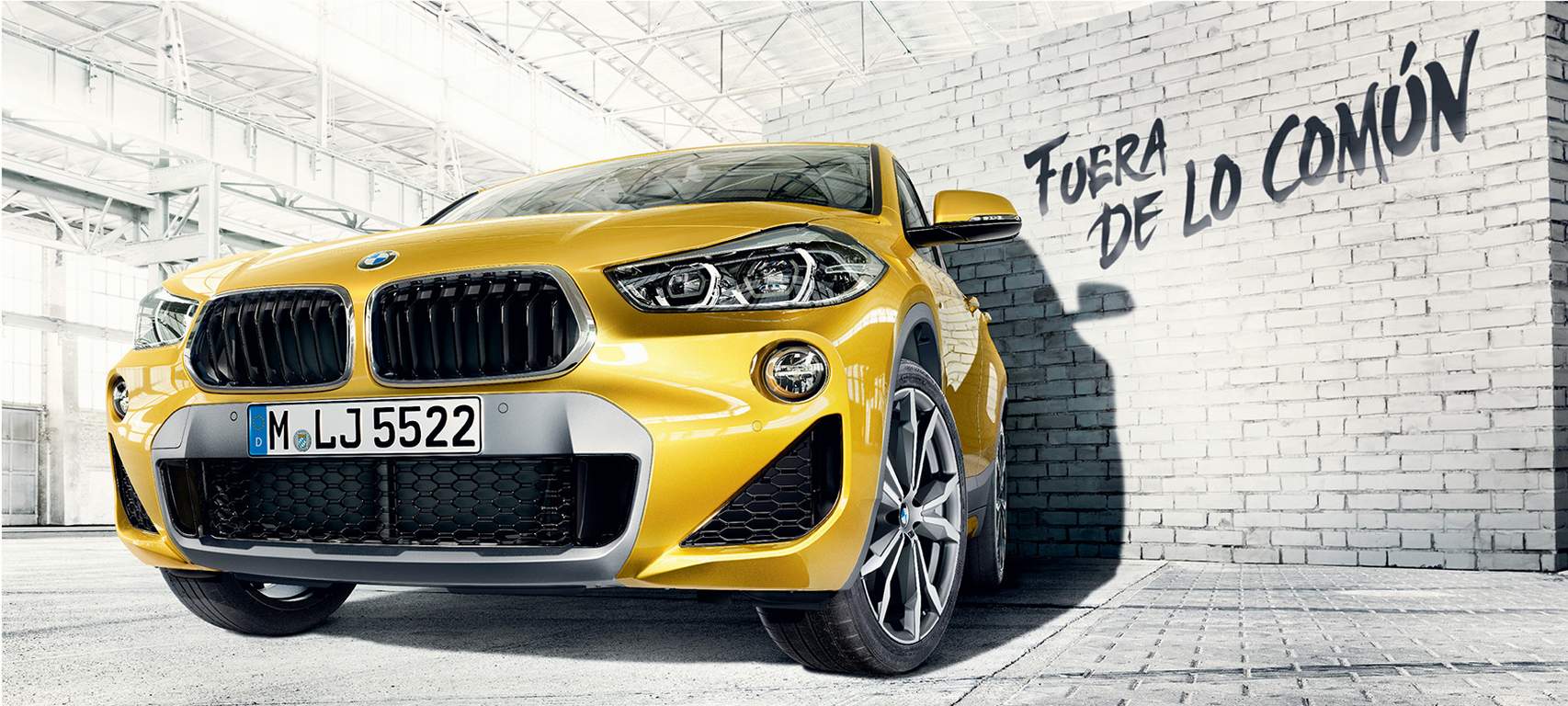
在現場實務目標操作與實際操作對比方面,例如要檢查一個重達 25 噸的複雜零件(例如模具)可能會花費很長的時間。但時間就是金錢,但現在透過科技輔具的應用,檢查過程變得相當簡單,工具製造和工廠工程部的員工可以在三腳架上安裝標準平板電腦,平板電腦的內置攝像頭可生成該工具的圖像,然後 AR 應用可將該圖像與所訂購工具的 CAD 結構數據疊加在一起。
根據鑽孔以及其他表面特徵清晰等平均 50 個標準,工作人員可以看到是否已落實所有生產規格。在發生微小偏差的情況下,可在現場退件,因為及早檢測出問題,可以留出足夠的時間在工具送往組裝區用於後續組件前,進行退件動作。
此外,BMW 在慕尼黑工廠也採用了目標/現實對比方法。使用 AR 應用,專家們將預量產汽車作為標準,檢測此類汽車內的構建理念是否成熟,部件的安裝位置是否正確。例如,該系統能夠確定側壁(擋泥板)的尺寸是否正確,是否排氣系統安裝在正確位置,或者所有必要部件是否都已安裝好。
相關 CAD 數據的可視化只需幾秒鐘時間,多個零組件的數據可以根據需要組合併與平板電腦上的攝像頭圖像進行疊加,然後計算出各個部件之間的理想位置,並彰顯出重要的設計特徵。